Two years ago, global pharmaceutical company Pfizer, Inc., made the decision to retool almost half of its 1-million-sq-ft production, packaging and distribution facility in Rocky Mount, N.C. Facilitating that equipment replacement came with some significant challenges that ranged from access limits and environmental abatement to some strict limitations on timing. Specifically, the decommissioning and surgical demolition of this large area needed to occur amidst ongoing production and distribution activities. Pfizer selected Ramboll, a global leader in engineering, architecture and consulting, to manage the project. Based on experience working with Brandenburg on complex and intricate projects, Ramboll brought in Brandenburg as its preferred contractor to complete the work. It was a demanding effort that required every bit of the team’s skills in logistics, planning and demolition amidst a labyrinth of clean rooms, narrow hallways and distribution space.
Labyrinth Logistics
Early on, the Brandenburg team developed an execution strategy that would mitigate any hazards or disruptions to the plant. The early efforts focused largely on six specific areas that included four of the autoclave spaces and two of the production lines. Along with a thorough investigation and analysis of issues that might arise from the decommissioning of systems, the planners identified and mapped routes to remove demolition debris and recyclable scrap metals to avoid interference with plant maintenance work. Further, the comprehensive plan incorporated time to clean and ready areas for future service.
The initial retooling effort was conducted during a 10-day holiday outage, a time when production was halted for maintenance. During this outage, two separate 20-person Brandenburg crews, each working a 10-hour shift per day, stepped through the highly detailed demolition plan. Nicolas Biciocchi, Brandenburg’s onsite superintendent, states, “A few of the biggest challenges were that the Pfizer production group was unsure when areas would be available, so our crews needed to be fluid about what work would be performed and in what sequence. As an additional challenge, the work started as the Covid virus was still spreading, so daily testing and other protocols were required. An outbreak would have halted the work and possibly affected pharmaceutical production.” The first step was to identify, colorcode and isolate all live utilities, a major concern for the safety of the demolition team. The process included air gapping, disconnecting and removing hundreds of utilities, including electric, compressed air, water and product lines. The removal was necessarily surgical and methodical to accommodate the tightly packed areas and the narrow corridors. The use of torches to facilitate removal (hot work) was limited due to air quality concerns, so the majority of the removal was completed using mechanical removal (cold cutting) techniques. When hot work was needed, the team relied on containment and air handling systems to exhaust any emissions.
A Clean Sweep
Once the utility work was completed, the team began work on the demolition of two major production and packaging areas. These areas spanned over 200,000 sq ft of floor space and were densely packed with equipment, utilities, conveyors, etc., and included the removal of seven slip sheet machines. Removal in these areas also included non-load-bearing concrete masonry walls and mezzanines. A significant feature of one area was a sterile room autoclave that was 200 ft long with a 15-ft diameter made primarily of stainless steel.
Once the demolition of the main floor and drop ceiling was completed, the removal of asbestos-containing materials (ACM) began. One area had several thousand feet of asbestos-coated ductwork. Brandenburg self-performed the removal of ACM ductwork. To date, 1,300 tons of ferrous and nonferrous metals have been recycled from these areas and more than 195,000 labor hours have been worked without injury or incident. Ramboll Project Executive Robert Patullo, states, “At Pfizer, the most important part of project execution is safety. Pfizer, Ramboll and Brandenburg have worked as a team to make sure the work is done safely and will continue to make safety the most important aspect of the project.
Work on the plant retooling continues. The Ramboll/Brandenburg team is already working on a plan to retool another production area with the same challenges faced as the previous two areas. That work is expected to take place during a scheduled outage in late 2023.
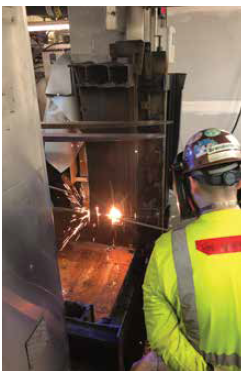